How Is Laminated Glass Made?
Laminated glass is made by fusing together plies of glass and interlayers to create a single sheet. For domestic windows, laminated glass usually comprises two plies of annealed glass and a ply of PVB for the interlayer.
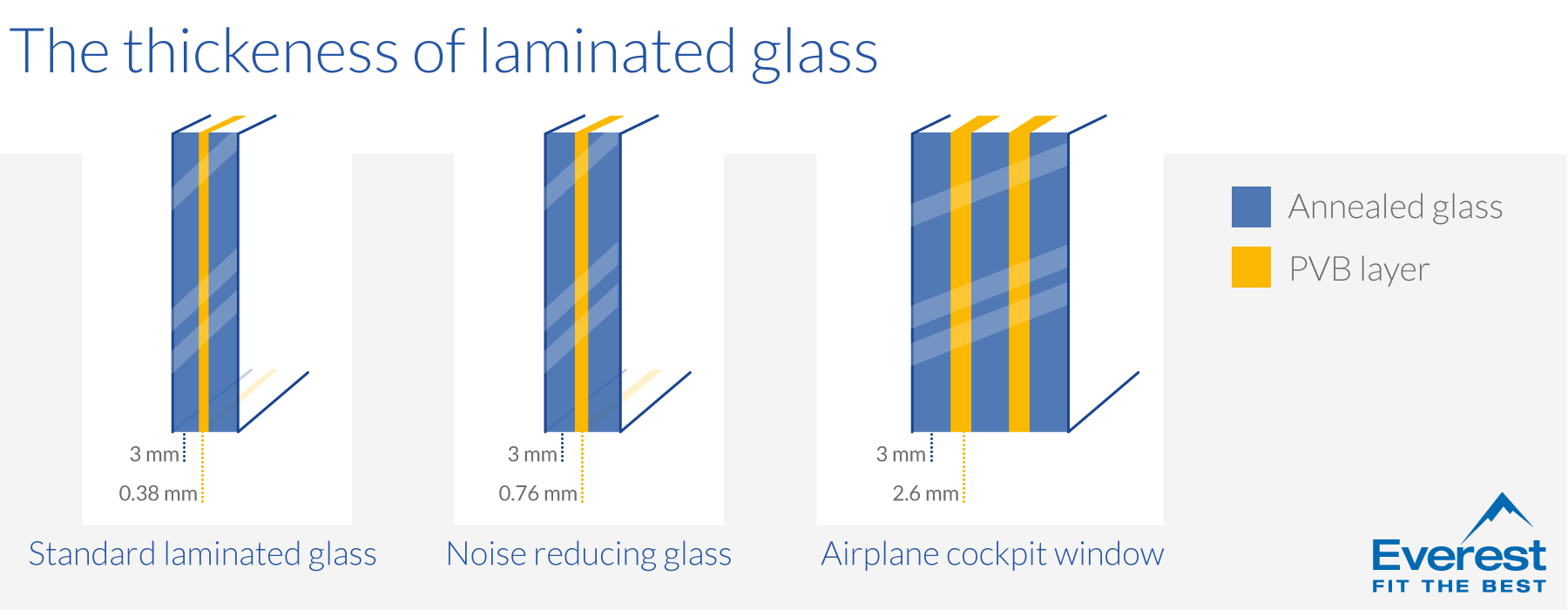
Laminated glass can be manufactured in many ways for differences in the final product:
- Glass used (standard annealed, toughened)
- Thickness and number of plies
- The interlayer material (PVB is the most popular)
- Special coatings on the piles (i.e. for solar gain)
For security purposes, the glass can be made in different thicknesses with different interlayers specifically for either:
- Bullet resistance
- Forced entry resistance
- Blast resistance
The layers or plies are assembled together in a controlled environment and vacuum extraction removes the air between the layers. The sheet is heat treated, compressed and then placed in an autoclave before final inspection.
The PVB interlayer used for domestic laminated glass is made in multiples of 0.38mm with standard thickness being 0.76mm and 1.52mm.
For non-domestic uses, the glass can be made from multiples of plies with different types of interlayer material in different thicknesses. For example, the cockpit of an aeroplane has five plies fused together and the interlayer ply is 2.6mm thick compared to 0.38 of a standard domestic window. Bulletproof glass has a polyurethane interlayer 1.25mm thick.
The different interlayers all have their own unique properties and are used for different end uses of laminated glass:
Interlayer material | Cost | Used for |
---|
Polyvinyl butryl (PVB) | £ | Domestic windows Windscreens Commercial shop fronts Glass balustrades Blast-resistant glazing |
Ionomer | £££ | Windows subject to impact Large unsupported glass panels Overhead canopies |
Ethylene-vinyl acetate (EVA) | £ | Solar panels Swimming pools |
Poured resin (CIP) | ££ | Curved or patterned glass Architectural glass |
Polyurethane (TPU) | ££££ | Bulletproof glass |
Source
At Everest, we have two types of laminated glass
Standard laminated | Nose reducing glass |
---|
Two plies of 3mm annealed glass | Two plies of 3mm annealed glass |
One ply of 0.38mm PVB interlayer | One ply of 0.76mm PVB interlayer |
Which Is Stronger Toughened or Laminated Glass?
Laminated glass and toughened glass have their own unique properties and use. They are often confused, but they are two very different products.
Toughened glass is heat treated to be four/five times as strong as standard annealed glass. To compare laminated glass against toughened glass in a strength test based on breaking point, toughened glass is stronger. But, once it breaks, it will break into small granular pieces.
Once laminated glass breaks, it is held together on its PVB interlayer and stays in place. It's very difficult to pierce through laminated glass because of the PVB core. Effectively, laminated glass can be considered stronger overall, but in a different way.
When choosing between laminated and toughened glass you have to consider how the glass will be used and what is the predominant safety issue.
For security reasons, laminated glass is by far the superior product, especially for manual or forced attack. The interlayer will hold the glass together under exceptional circumstances and is used for jewellers' windows or bulletproof car windows to avoid penetration.
Where there is a danger of falling glass from overhead skylights or balustrades, laminated glass must be used.
In a domestic window, toughened glass is more resistant to actually breaking but it will shatter into small granular pieces to avoid injury. If security is not an issue, toughened glass is better for glazing in critical areas.
It's also possible to combine toughened and laminated glass for a glazing product that has a high breaking point and is difficult to pierce. This would be ideal for a glazed external door, where safety and security are both important.
Note that both laminated glass and toughened glass can meet safety requirements for glazing in critical areas.
How Laminated Glass Works for Sound Reduction
Laminated glass is used in noise reduction windows as it helps to dampen the sound.
Noise reduction windows can reduce soundwaves because they have a gap between the panes of glass filled with Argon gas that reduces the transmission of the wave.
By using a laminated layer on one pane of glass in the double-glazed unit, the panes have different widths and this is enough to cause the panes to oscillate at different vibrations.
The difference in frequency disrupts the soundwave and reduces the transference of noise through the glass. The PVB laminated layer can also dampen the sound transference through the pane of glass.
All of these factors combined can help to reduce noise by up to 40 dB.
How Laminated Glass Works for UV Resistance
Laminated glass also has the benefit of reducing UV light transmission.
UV bleaching is also known as colour fading or photodegradation, where ultraviolet light causes a change in molecular structure that reduces pigment.
Sunlight, as warming and uplifting as it is, can cause damage to fabrics, furnishings and floors where the intense light shines. Wooden floors can warp, leather settees crack and artwork can fade. This is especially a problem for windows that face south or southwest and are exposed to sunlight at its most intense during the day.
The PVB layer in laminated glass does reduce UV transmittance considerably compared to standard glass and helps to protect furniture and furnishings.
Glass | UV transmittance (%) | |
---|
6mm clear | 57 | |
6mm blue-tinted | 18 | |
6.4mm clear laminated | 3 | Everest standard laminated glass |
6.8mm clear laminated | 1 | Everest noise reduction glass |
7.5mm clear laminated | 0 | |
Source
It's worth noting that for valuable paintings or antiques, they can still be susceptible to even normal levels of daylight. In cases of precious artworks, they should be stored in darkness away from normal light.